Polypropylene is considered the “steel” of the plastic industry. It can be customized and adapted to various fabrication techniques, making it effective for a dizzying array of applications. In fact, behind polyethylene it’s the second most common plastic for production. The reason why polypropylene is so widely used in manufacturing is because no other plastic has its unique blend of properties that make it so versatile.
The best way to illustrate the value of polypropylene is through one of its most popular applications: the “living hinge.” You’ve seen that thin, plastic hinge that attaches the lid to a bottle of ketchup, for instance. Polypropylene is the secret to any flip-top bottle because even with very little material, you can bend it over and over without breaking. It has a range of motion close to 360 degrees.
Properties of Polypropylene
Why are companies so enamored with polypropylene? Its specific qualities make it even more clear. Here’s how it breaks down:
- It’s inexpensive. Is it the most important thing when it comes to quality plastic product manufacturing? Of course not. But it’s one of the top considerations.
- It’s available. There are no long waits for the material to ship or higher prices due to rarity. You want it? You got it.
- It has good fatigue resistance. This is the reason for living hinges. Bend it, flex it—polypropylene will retain its shape despite wear and tear.
- It’s a thermoplastic. This classification is about how it responds to heat (as opposed to “thermoset”). Polypropylene can be heated to its melting point—around 130 degrees Celsius—and then cooled. When it’s reheated after that, it suffers no notable degradation. Thermoset plastics can only be heated once.
- It has a slippery surface. Polypropylene can be used for low friction applications such as gears.
- It’s flexible. This is due to the fact that it’s semi-crystalline.
- It’s lightweight. Polypropylene’s low density results in weight savings for both manufacturers and distributors.
- It’s resistant to absorbing moisture. This makes it viable for products and parts that need to be waterproof.
- It’s resistant to chemicals. This applies to a wide range of diluted bases, acids, oils, and solvents, making it ideal for making containers for liquids such as cleaning supplies.
- It has good impact strength. Ithas the ability to bend on impact, but also has impressive tensile strength—around 4,800 psi.
- It can be copolymerized. Polypropylene is especially versatile because it can be combined with other plastics into a composite.
- It’s great as an electrical insulator. Polypropylene’s high resistance to electricity opens up all kinds of applications for electronic components.
- It’s transmissive. Because polypropylene is naturally opaque, it can be made transparent if there’s a need to transfer electromagnetic energy as light. It’s also aesthetically attractive.
- It’s better for the environment. Polyethylene has the smallest impact among all plastics. It produces less solid waste by weight as well as less CO2 equivalents than PET, PS, or PVC.
Two Different Types
Polypropylene is divided into two categories. Here’s how they compare:
Homopolymer
This is the most commonly used form. It’s a monomer in a semi-crystalline, solid state.
Copolymers
This family is further broken down into another two kinds.
- Polypropylene random copolymer combines ethene and propene. The ethene units are incorporated randomly into the polypropylene chains, making the polymers flexible and clear.
- Polypropylene block copolymer has more ethene content. The co-monomers are arranged in regular patterns or “blocks.” This makes the plastic tougher and less brittle than the random version. This type is used for high-strength applications, such as industrial usages.
Comparison To Polyethylene
Polypropylene has properties significantly similar to polyethylene, especially when it comes to solution behavior and electrical resistance. However, there are two major differences. Polypropylene is stiffer than polyethylene and has a much higher melting temperature.
A Few of Its Applications
There’s no need to limit the uses for polypropylene to just a few categories, but these can show how valuable the plastic is for various industries.
Medical
Polypropylene has been a miracle plastic for the health industry. It’s present in laboratories in many forms, particularly in sutures for surgery. Polypropylene is what makes up the synthetic, non-absorbable suture marketed as Prolene. Doctors and surgeons can operate on the patient with instruments and devices made of polypropylene, and then start the healing process with sutures also made of it. In addition, the material is used for tools, equipment, containers, and more.
Packaging
If you have plastic food containers that don’t melt in the dishwasher—from Rubbermaid or Sterilite—they’re probably polypropylene. As packaging, polypropylene can work in different ways. In its flexible form, it can replace cellophane and paper. When rigid, it’s used for caps, bottles, and jars, among many other things.
Automotive
Because it’s inexpensive, is weldable, and has suitable mechanical properties, the auto industry has learned that polypropylene is a better choice for parts than traditional metals. It can be found in bumpers, fender liners, battery cases, trays, instrumental panels, and so on.
Clothing
Polypropylene is everywhere because it can take on yet another key form: fibers. It’s extremely valuable to the clothing, fashion, and sports industries because it’s so resilient—it resists wear and tear, the sun, mold, bacteria, and water. It’s idea for activewear for outdoor sports, as well as equipment and accessories. These fibers can keep you warm as a base layer in the winter, and cool in the summer with moisture-wicking abilities. You can even personalize this kind of polypropylene, which is what makes it such a popular choice for promotional tote bags.
Recent Publicity
Polypropylene has been in the news over the past year for one essential application: non-medical face masks. Fabric masks have been popular but require an additional filter to be effective. Experts recommend industry-grade “spunbound” polypropylene as the middle layer in cotton masks with a pocket.
One of the reasons polypropylene is ideal for masks? It holds an electrostatic charge. In this situation, static cling—usually considered an annoyance—traps droplets coming in or out of the mask. Polypropylene is also water-repellent, so virus particles aren’t able to use moisture and stay viable. It’s just one more way that this plastic is proving its worth and versatility.
At Miller Plastics, we’ve learned exactly why polypropylene is so widely used in manufacturing. It’s not right for every project, but we can tell you if it’s the highest-quality, lowest-cost way to create your custom parts. Contact us for more information on the best materials for production.
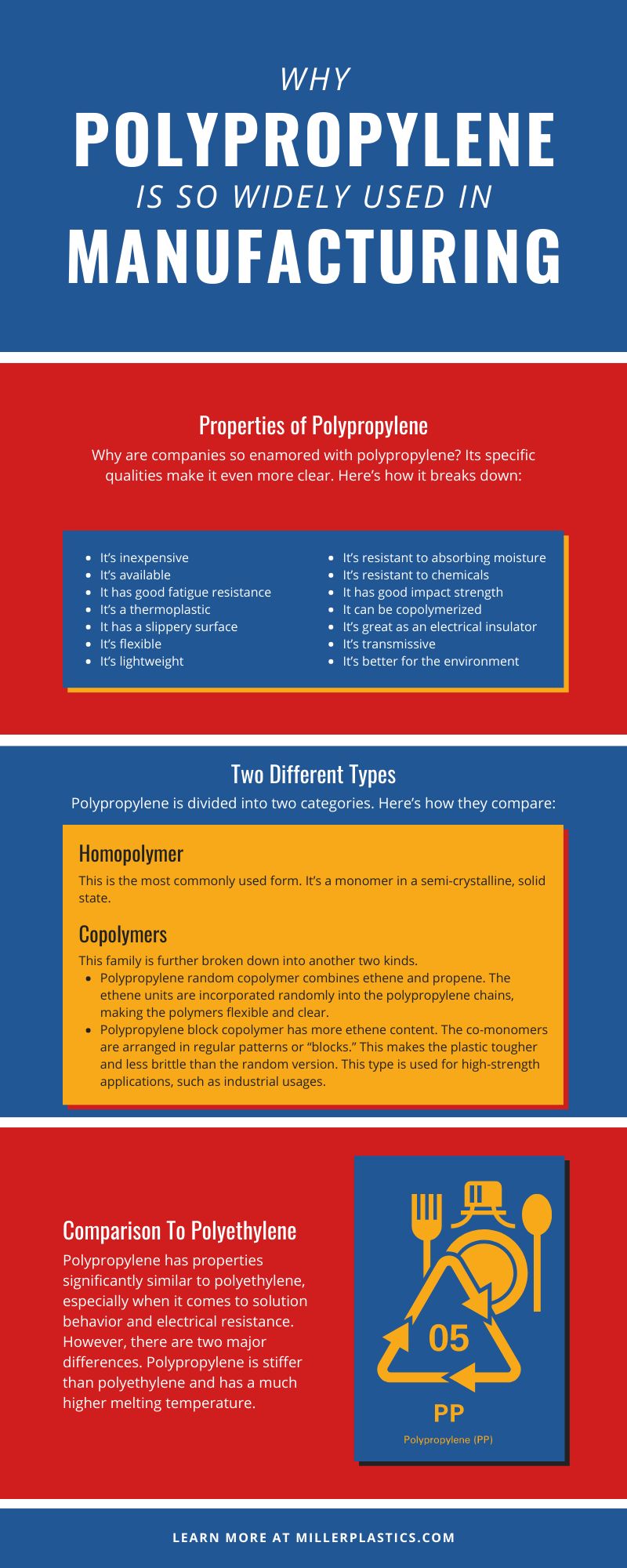