Every product designer faces a pivotal choice when crafting new items—should you choose stock parts or custom plastic parts for product design? This decision can influence everything from production timelines to cost-effectiveness and the final product’s quality.
For many designers, the allure of stock parts lies in their immediate availability and potentially lower costs. On the other hand, custom parts offer the promise of perfect alignment with unique design specifications. In this guide, we’ll explore the nuances of both options and help you determine the best path for your next project.
Understanding Stock Plastic Parts
Stock plastic parts are pre-manufactured, standardized components readily available for use. These parts often make sense when you’re aiming for a quick turnaround or need to maintain a tight budget. They’re typically mass-produced, which allows manufacturers to sell them at a lower price point.
However, this affordability often comes with limitations. The designs of stock parts are pre-set, which means they may not fit seamlessly into your product’s unique design. While stock parts can speed up production processes, they might require compromises on the final product’s aesthetic or functionality.
In certain industries, stock parts can be a boon. For example, if you’re working on a product that doesn’t demand unique dimensions or specific design features, then choosing stock parts can be advantageous. Stock components are common in electronic, automotive, and household goods due to their standardized nature. Before making this choice, weigh the potential design limitations and consider whether stock parts can truly meet your product’s specific needs.
Exploring Custom Plastic Parts
Manufacturers tailor custom plastic parts precisely to a designer’s specifications. This level of customization allows for greater flexibility and creativity, enabling designers to create unique, innovative products. Manufacturers craft custom parts using specific materials and processes to meet the exact requirements of your design. This tailored approach can lead to products that stand out in the market and offer a competitive edge in terms of functionality and aesthetics.
Opting for custom parts often involves higher costs and longer lead times. The manufacturing process can be more complex, as it typically requires the creation of molds and prototypes. This can extend the timeline of your project, which might not align with every product development strategy. Despite these potential drawbacks, the ability to create a truly original design may outweigh the additional time and cost.
The Role of Material Selection
When deciding between stock and custom plastic parts, material selection plays a significant role. Stock parts usually contain widely used plastics such as polyethylene or polypropylene. These materials are versatile and cost-effective but may not offer the performance characteristics you need for specialized applications. Custom parts, on the other hand, allow for the selection of high-performance materials tailored to specific environmental or operational conditions.
For example, if your product requires resistance to extreme temperatures or chemicals, custom parts made from specialized plastics like PTFE or PEEK might be necessary. These materials can enhance durability but at a higher cost. Understanding the material requirements of your product is crucial in determining whether stock or custom parts will best meet your needs.
Production Efficiency and Timelines
Choosing between stock and custom plastic parts can significantly impact your production timeline. Stock parts offer immediate availability, which reduces lead times and helps to accelerate the manufacturing process. This can be particularly beneficial for projects with tight deadlines or when quick market entry is a priority.
On the other hand, custom parts require a more involved production process that includes design, prototyping, and testing phases. This can extend timelines and provide the opportunity to refine and perfect the product. If your project allows for a longer development period, then investing time in custom parts can lead to a more refined and functional end product.
Cost Considerations in Part Selection
Budget constraints are a common concern in product design, and the choice between stock and custom parts can have financial implications. Stock parts are generally more affordable due to mass production and standardized designs. This makes them an attractive option for projects with limited budgets or those where cost efficiency is a primary concern.
Custom parts, while potentially more expensive, offer the potential for long-term savings. They can reduce the need for additional modifications or adjustments during the product development cycle. Investing in custom parts up front can prevent costly redesigning down the line. However, you should weigh these potential savings against the initial investment required for customization.
Balancing Quality and Design Integrity
The quality of plastic parts can significantly influence the success of your product. Stock parts may compromise design integrity due to their standardized nature. While manufactured to meet general quality standards, they may not align perfectly with your specific design needs. This can lead to challenges in maintaining the intended design and functionality.
In contrast, manufacturers design custom parts to meet precise specifications, which ensures a high degree of quality and design integrity. Working closely with a plastic products manufacturer can provide the expertise needed to create parts that align with your vision. This collaboration can enhance the overall quality and performance of your product, ensuring it meets or exceeds market expectations.
Innovations in Plastic Manufacturing
Advancements in plastic manufacturing technologies continue to expand the possibilities for both stock and custom parts. Innovative processes such as 3D printing and injection molding offer new opportunities for designers to create complex, intricate designs. These technologies can enhance the precision and efficiency of the manufacturing process, which reduces lead times and improves product quality.
For custom parts, innovations in manufacturing can streamline the prototyping and production phases, enabling faster iterations and reducing costs. Stock parts can also benefit from these advancements as new materials and techniques become available. Staying informed about the latest developments in plastic manufacturing can help you make the best decisions when selecting parts for your product.
Choosing between stock and custom plastic parts in product design involves weighing factors like cost, quality, and design flexibility. While stock parts offer affordability and quick turnaround, custom parts provide tailored solutions for unique product specifications. Either option can be beneficial depending on your project’s needs and goals.
For expert guidance on your plastic part needs, reach out to Miller Plastic Products and discover how we can support your product development process. We use state-of-the-art equipment to provide you with custom options that meet your needs.
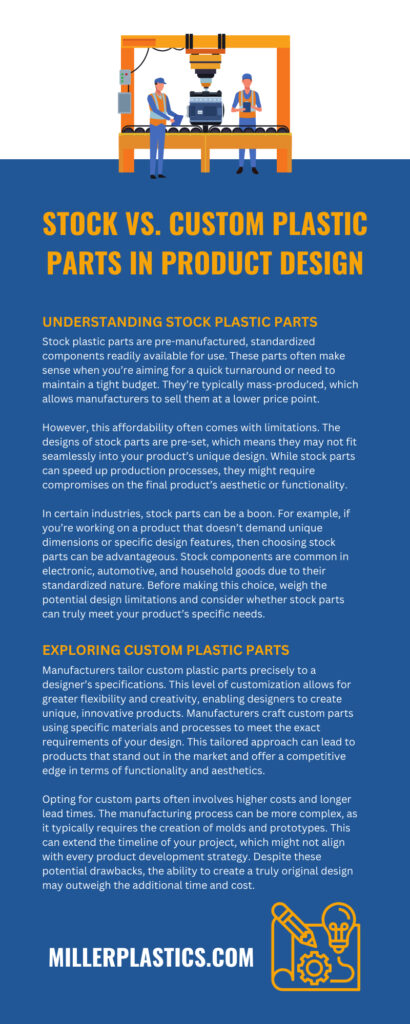