Quality Polypropylene Valves & Fittings | Plastic Pipe Fabrications
Plastic Pipe Fittings Design, Engineering, Fabrication & Machining
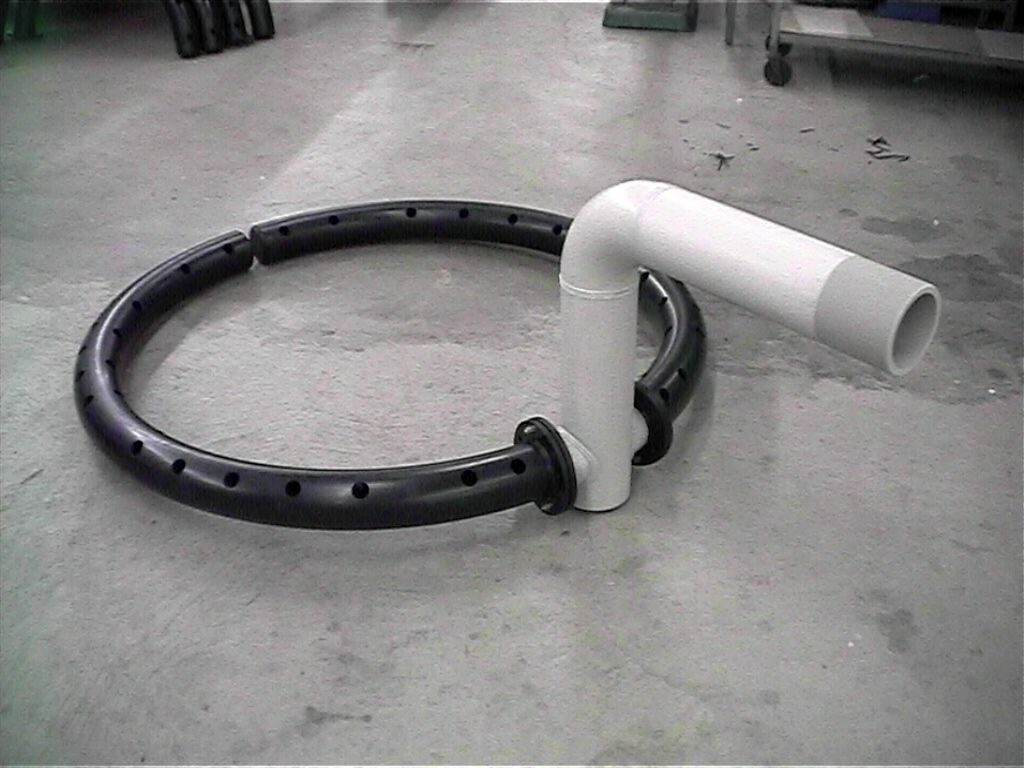
As one of the top polypropylene pipe system fabricators in the USA, Miller Plastic Products provides standard and custom solutions to suit your specific application and environmental needs. We can create the polypropylene valves and fittings you need as well as other types of custom plastic pipe fittings made to your specifications.
We carry great expertise in working with many materials and have a deep understanding of the various requirements plastic pipe fittings and polypropylene pipe fittings must meet. So, in short, you’ll get the functionality, durability, and performance you need in your plastic pipe system. Reach out to Miller Plastic Products today to learn more about our plastic pipe fittings as well as the rest of our plastic manufacturing services.
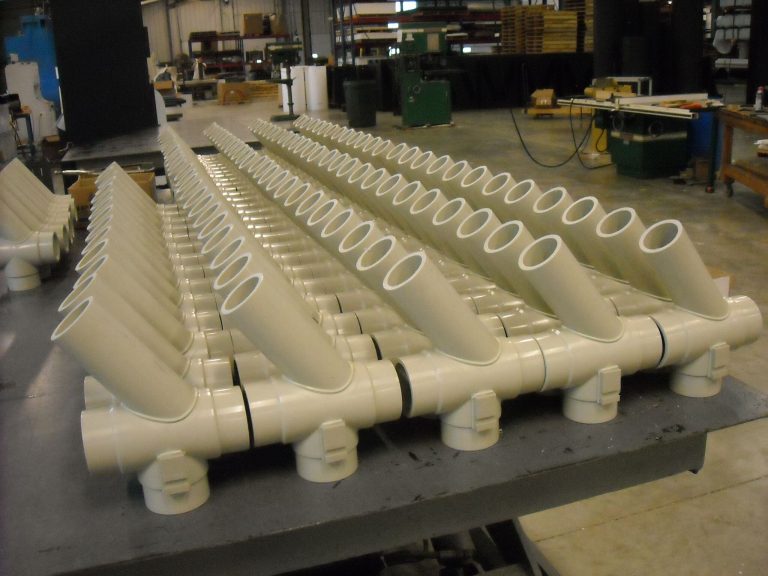
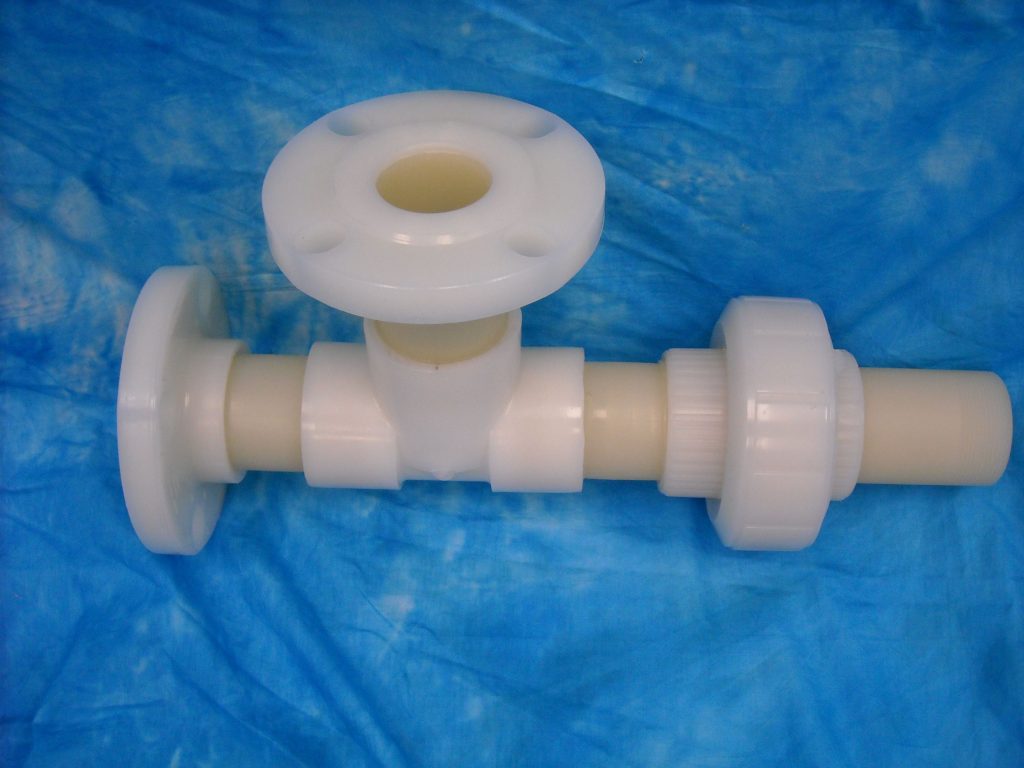
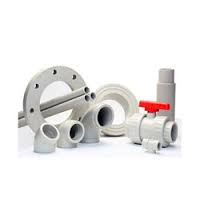
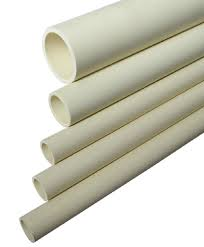
We actively work with you to ensure your custom plastic pipes and plastic pipe fittings meet or exceeded requirements for:
- Thermal Conductivity
- Thermal Expansion
- UV Resistance
- Longevity of Performance
- Chemical Resistance
- Thickness
- Size
- Diameter
- Structural Integrity
- Any other polypropylene pipe properties you require
Some of the Materials We Work With Include:
Our polypropylene pipe systems, valves, and fittings are widely used throughout the industrial processing markets
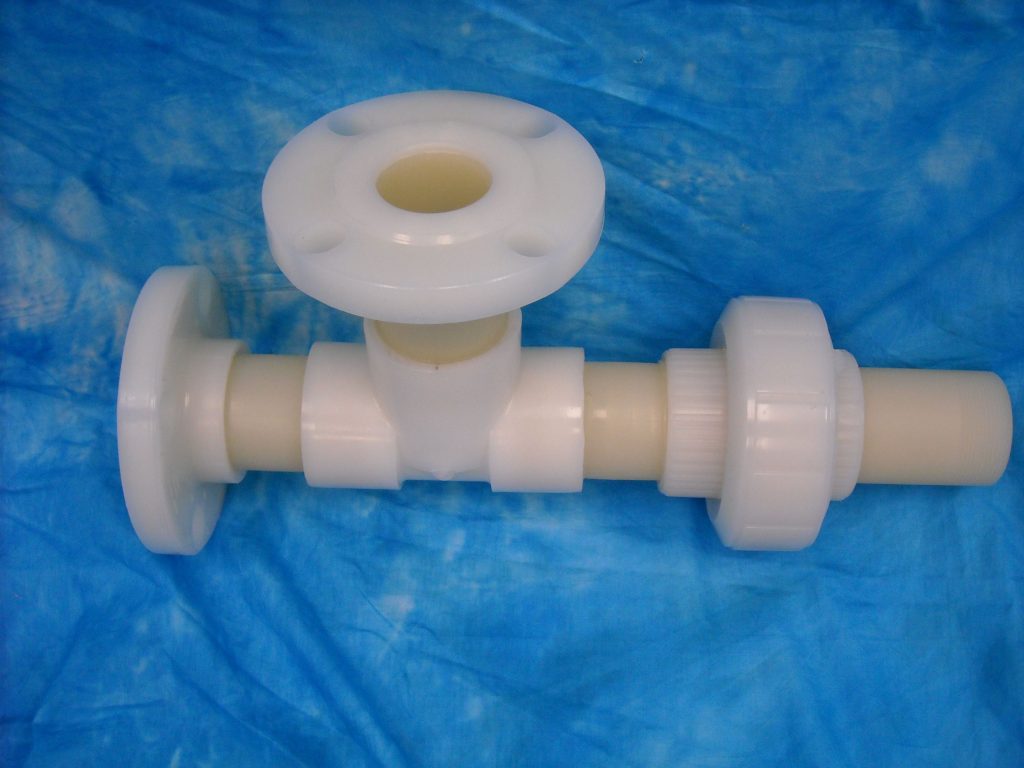
We provide polypropylene piping systems for drainage, natural gas, ventilation and more.
Polypropylene piping systems are desired for their lightweight properties, abrasion resistance, high impact strength, and reliability in heat fusion welding, as well as its thermal and electrical insulation properties.
Polypropylene piping systems are also revered for their superior chemical resistance, which makes them resistant to many organic solvents, including acids, alkalis, and salts.
The maximum temperature for working-use polypropylene pipes is 90ºC (194ºF); however, it can endure short-term use up to 110ºC (230ºF). Polypropylene piping systems can be assembled by means of heat fusion welding, butt fusion, or through electrofusion fittings, socked-ended fittings or threaded fittings.