Monomers, the tiny, powerful building blocks of plastics, are the unsung heroes of the modern materials world. For engineers and manufacturers working with plastics, an understanding of monomers is foundational. Knowing what they are and how they work makes it easier to produce useful products that consumers will want. Learn more about monomers, what they are, and the crucial role they play in plastic machining.
What Are Monomers?
Monomers are individual molecules that, when combined, form a polymer. The term monomer comes from the Greek “mono,” meaning one, and “meros,” meaning part. These simple molecules polymerize, or bond, to form the complex polymers that we know as plastics.
History of Monomers
The discovery and understanding of monomers date back to the early 1800s. Notably, the work of August Wilhelm von Hofmann, who first coined the term monomer, was instrumental in recognizing the significance of these compounds in the polymerization process. As the study of chemistry and material science advanced, the role and impact of monomers in everyday materials became increasingly clear. Today, manufacturers in all different sectors rely on monomers for plastic packaging, parts, and components.
Attributes of Polymer Materials
You can define the attributes of polymer materials according to the monomers manufacturers synthesize them from and the details of the polymerization process they undergo. Here are some examples of these attributes:
- Tensile strength: This defines how much the material can stretch before it breaks. Varying the polymerization method and the type of monomer can significantly alter a plastic’s tensile strength.
- Thermal stability: Some polymers withstand high temperatures without deforming. This property is crucial for plastics used in high-temperature environments or applications like cooking utensils or car parts.
- Chemical resistance: Certain monomers can give plastics the ability to resist degradation due to chemical exposure, making them suitable for use in harsh chemical environments.
- Electrical insulation: Many plastics are used for their non-conductive properties, providing insulation in electrical applications. The choice of monomers can ensure that the resultant polymers have these insulating characteristics.
The specific combination and ratio of monomers, along with the conditions under which polymerization occurs, result in plastics with a wide range of properties, allowing for use in many different applications.
Types of Monomers
There are a wide variety of monomers used in plastic production, which can be categorized based on their chemical structure and source. Some of the most common types include:
- Ethylene and propylene: Important for producing polyethylene (PE) and polypropylene (PP) plastics.
- Vinyl chloride: Used in the synthesis of polyvinyl chloride (PVC).
- Styrene: A key monomer in the production of polystyrene (PS) and styrene acrylonitrile (SAN) plastics.
- Acrylic: Found in polymethyl methacrylate (PMMA), often referred to as acrylic glass or by the trade name Plexiglass.
- Tetrafluoroethylene: The monomer for polytetrafluoroethylene (PTFE), commonly known by the DuPont brand name Teflon.
- Siloxanes: Building blocks for silicones, a diverse family of synthetic polymers.
Each type of monomer brings distinctive characteristics to the resulting polymer, influencing properties such as flexibility, hardness, and resistance to temperature and chemicals.
Role of Monomers in Plastic Machining
Understanding the role of monomers in precision plastic machining requires a look at the polymerization process and the formation of polymer chains.
Polymerization Process
Polymerization is the chemical process through which monomers combine to form polymers. It can occur through various means, including addition polymerization, where unsaturated monomers combine together on a growing chain, and condensation polymerization, which releases a small byproduct, such as water or alcohol, as two molecules combine. The choice of polymerization method impacts the properties of the resulting plastic.
Formation of Polymer Chains
As monomers react and link together, they form long strands known as polymer chains. These chains give plastic materials their unique structure, which can be linear, branched, or cross-linked. The length and configuration of these chains are critical, as they ultimately determine the material’s mechanical and physical attributes.
Influence on Mechanical Properties
By altering the type and amount of monomers used, manufacturers can manipulate the mechanical properties of the plastic. Monomers with larger molecular weights generally produce stronger and more rigid materials, while smaller monomers contribute to flexibility.
Impact on Machining and Processing
During the plastic machining process, the choice of monomers affects the material’s machinability. It can influence factors such as:
- Melt flow index (MFI): The ease at which the material flows during processing.
- Thermal conductivity: Determines resistance to heating and cooling during machining.
- Surface energy: A characteristic linked to adhesion and compatibility with other materials.
The extensive role of monomers in plastic machining is apparent throughout the polymerization and processing stages, shaping each final product’s form and function.
Applications and Examples
Plastics are ubiquitous in modern life and used in a staggering array of applications. Here are a few examples where monomers play a crucial role:
Pipe Installation Systems
PVC and high-density polyethylene (HDPE) pipes are useful materials in construction and infrastructure projects. The monomers used to make these materials influence their durability, flexibility, and resistance to corrosion, making them ideal for a range of applications, from water distribution to gas transmission.
Medical Equipment
Plastics like polycarbonate and various acrylates are essential for manufacturing medical equipment due to their transparency, durability, and ability to withstand sterilization processes. The monomers involved in producing these plastics have to meet stringent health and safety standards.
Automotive Components
With the automotive industry continually pushing for lightweight yet robust materials, plastics are increasingly replacing traditional metals. Monomers contribute to the production of impact-resistant bumpers, lighter-weight interior components, and fuel-efficient engine parts.
Packaging and Consumer Goods
Perhaps the most visible use of plastics is in packaging materials and consumer goods, which depend on monomers to provide specific barrier properties, color, and texture. Common examples include polyethylene terephthalate (PET) for beverage bottles and polystyrene for disposable cutlery and food packaging.
This wide range of applications demonstrates the versatility of plastics, all rooted in the strategic use of monomers during manufacturing.
Meeting the Unique Demands of Society
Monomers provide the foundation for a material that has revolutionized countless industries. From the pipes running underground to the components in our cars, plastics are integral to our daily lives. Understanding monomers, what they are, and their role in plastic machining enhances our appreciation for these materials and opens doors to innovation and improvement in how we utilize and recycle them.
As developments in material science continue, monomers will become increasingly sophisticated, with manufacturers tailoring plastics to meet the evolving demands of society and the natural world. They are the silent architects of the modern age, and their legacy, embodied in plastics, is worth exploring and understanding.
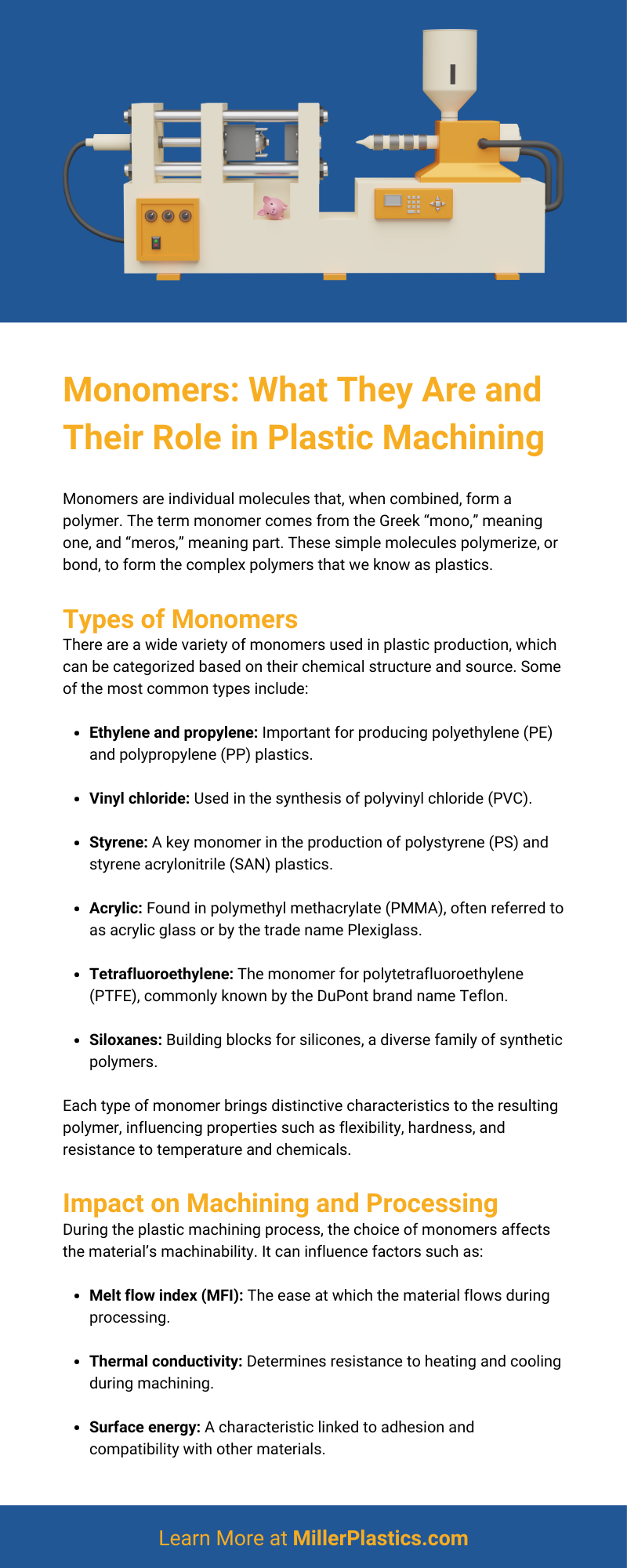