Proper chemical storage is a top priority for industries that rely on compliance with Environmental Protection Agency (EPA) regulations. Neglecting these guidelines can lead to safety risks, financial penalties, and environmental harm.
This guide explains EPA guidelines for plastic chemical tank storage. Learn how you can confidently manage your storage needs while ensuring the safety of your operation and surrounding ecosystems.
Understanding Secondary Containment Requirements
The EPA sets clear storage guidelines for chemicals, and secondary containment is among the most important. A secondary containment system serves as a backup in case a spill or tank failure occurs. This means your primary plastic tank will catch and secure any leakage, preventing it from contaminating the soil or water.
To meet these guidelines, secondary containment needs to be the proper size and capable of holding at least 110 percent of the largest tank’s capacity. Materials used for containment should also be compatible with the chemicals being stored. An inadequate containment system not only fails to meet EPA standards but also increases safety risks for your facility.
When choosing a secondary containment system, investing in a design tailored to your chemicals’ properties provides the best risk management. Double-walled plastic tanks are a common option that offer integrated containment to meet compliance standards.
Compatibility Is Key to Plastic Tank Selection
Not all plastics work for every chemical. EPA guidelines emphasize the importance of material compatibility in plastic chemical storage tanks. Chemicals that aren’t stored in compatible tanks can react with the tank material, causing corrosion, degradation, or leaks. This not only puts your materials at risk but also increases the likelihood of enforcement penalties.
For example, high-density polyethylene (HDPE) tanks are typically recommended for a wide range of chemicals due to their durability. However, certain harsh acids or solvents may require tanks made of specialized plastic blends.
Checking compatibility charts supplied by tank manufacturers can provide valuable insights. Performing this due diligence upfront will save you operational headaches in the long run.
Proper Ventilation To Prevent Pressure Buildup
Another key aspect of EPA guidelines involves adequately ventilating plastic chemical storage tanks. Chemicals inside these tanks can produce gases or vapors, which lead to pressure buildups if the tanks don’t have proper ventilation.
Failure to maintain proper ventilation increases the risk of chemical spills, tank damage, and even explosions. Relief vents and fittings are essential to allow gases to escape safely. Additionally, EPA regulations stress using closed systems where possible to minimize harmful emissions.
Before installing your tanks, inspect them to ensure they have the right venting accessories. Periodic testing after installation will confirm everything is functioning correctly.
Location Matters for Proper Chemical Storage
EPA guidelines also place a strong emphasis on where you store your chemical tanks. Improper placement can increase risks of contamination if leaks occur, especially in sensitive locations like wetlands or near groundwater sources.
You should place your tank on a sturdy, level base to reduce the risk of tipping or uneven settling over time. You may need elevated platforms in some cases to optimize drainage or minimize exposure to flood hazards.
Becoming familiar with local zoning laws and EPA site standards can streamline your planning process. Keeping your tanks in a secure area, free from potential environmental factors, helps you stay in compliance.
Training Employees in Compliance Practices
Having a compliant storage setup is only part of the job. Employees interacting with chemical storage tanks need thorough training to follow EPA safety protocols. This includes understanding how to handle chemicals, report leaks, and maintain equipment.
Regularly scheduled training sessions are an effective way to bridge knowledge gaps and solidify safety procedures. Clear instructions and visual aids near storage areas can also serve as helpful reminders.
Including your entire team in compliance efforts reduces the risks of operational errors and regulatory violations. Empowering employees with knowledge benefits your workplace’s overall safety culture.
Accurate Spill Prevention and Response Planning
The EPA mandates that businesses with chemical storage need to prepare detailed spill prevention plans. These plans must anticipate potential worst-case scenarios and outline procedures to minimize environmental impact.
Presenting a well-documented Spill Prevention, Control, and Countermeasure (SPCC) plan isn’t just an administrative necessity. It’s a proactive tool for risk management. This includes identifying proper clean-up equipment and ensuring emergency access to secondary containment areas.
Routine drills assessing your spill-response plan reinforce readiness in the event of an actual situation. Being prepared prevents escalation and minimizes downtime following an emergency.
Regular Tank Maintenance Is Nonnegotiable
No matter how well you install your tanks, ongoing maintenance is critical according to EPA regulations. Inspections help identify early signs of wear, stress cracking, or external damage that could lead to leaks.
Most EPA guidelines recommend visually inspecting your plastic tanks monthly. Use checklists to document issues such as changes to structural integrity, missing fittings, or vent clogs. Early detection is key to avoiding larger repair bills or environmental damage.
Some businesses also rely on professional inspection services for peace of mind. This is especially beneficial for pressurized tanks or systems used to store hazardous materials.
Labeling for Safe and Compliant Usage
Proper labeling matters when it comes to adhering to EPA storage requirements. Every plastic chemical tank must clearly display its contents to prevent accidental misuse or mixing of incompatible substances.
Additionally, labels should highlight hazard warnings and storage temperatures where applicable. These labels must be visible and legible at all times, even in wet or extreme weather conditions.
Using durable labeling materials and regularly reviewing them for accuracy helps keep your facility compliant and safe. Teams should make checking these labels part of their inspection routines.
Partnering With Experts Simplifies Compliance
Managing EPA chemical storage requirements can feel overwhelming, especially for businesses with complex needs. That’s why partnering with a trusted plastic water storage tank manufacturer like Miller Plastic Products is a smart move.
Their expertise ensures custom tanks meet both your specifications and federal guidelines, giving you confidence in your setup. Access to a resourceful partner eliminates guesswork and optimizes your storage systems’ performance, helping your operation run smoothly for years to come.
A Smarter Way To Store Chemicals
Following EPA guidelines protects more than just the environment—it secures your investments and safeguards your team. Whether it’s secondary containment, diligent maintenance, or adopting technological advancements, compliance enhances every aspect of your operations.
If you’re considering upgrading your chemical storage, Miller Plastic Products can bring unparalleled quality with cutting-edge technology and a skilled team. Contact us today to create storage solutions that are as reliable as your business itself.
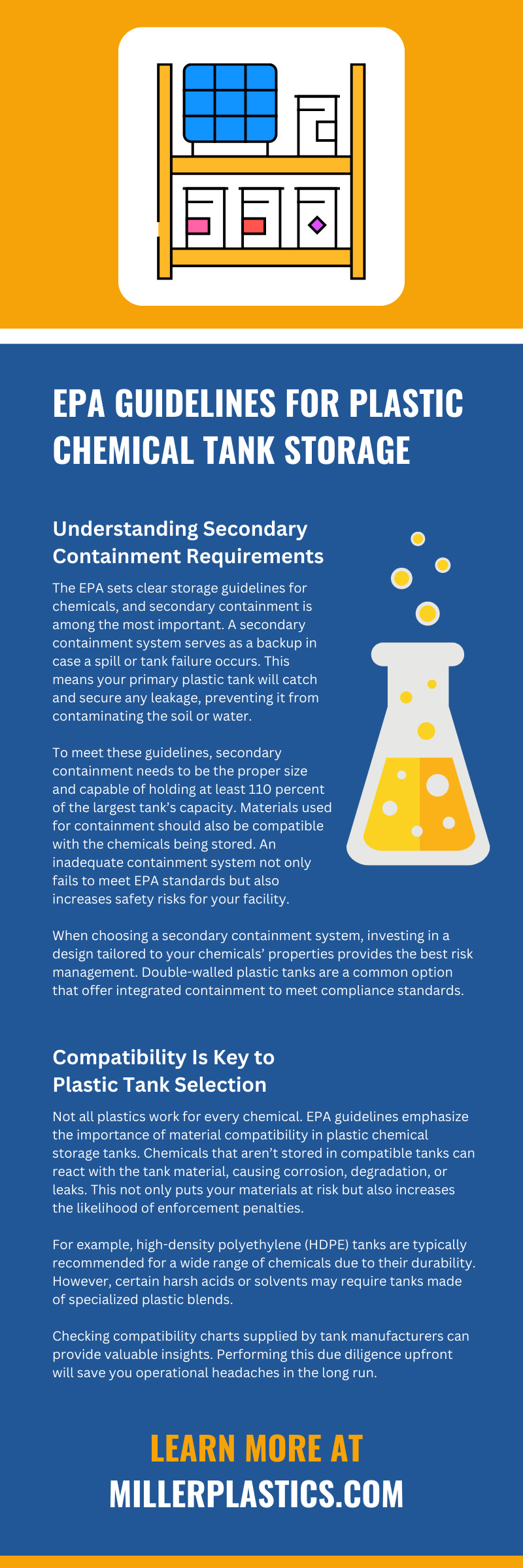