Gears are pivotal in countless industries, from manufacturing plants and pharmaceutical processing to plating line equipment. Traditionally, gears manufactured from metals like steel and aluminum have been the default choice due to their strength and durability. However, the increasing adoption of plastic parts, particularly plastic gears, has revolutionized how businesses maintain equipment and optimize efficiency.
This shift isn’t merely a question of cost; it reflects the evolving demands of modern engineering and manufacturing. Keep reading to learn more about the benefits of using plastic gear replacement parts.
Reduced Manufacturing Costs
One of the most compelling reasons to switch to plastic gears is their cost efficiency. Manufacturing plastic components is far less labor-intensive than metal. Manufacturers typically produce plastic parts through injection molding or 3D printing, unlike metals, which require shaping, machining, and heat treating.
This process reduces production time and costs associated with raw materials and workforce requirements. For industries running high-volume production lines, the financial benefits are almost immediate.
Improved Wear Resistance and Durability
Plastic gear replacement parts offer exceptional wear resistance, particularly when designed with advanced polymers. These materials are crafted to withstand the friction and pressure inherent in mechanical operations. Unlike metals, plastics possess natural self-lubricating properties.
This ability reduces the need for frequent lubrication, preventing downtime in production facilities such as pharmaceutical plants or food packaging lines. Further, plastics do not experience corrosion, giving them an edge in moisture-heavy environments like plating lines or food processing.
Lightweight Advantage
The weight of a gear directly impacts the efficiency of the machinery it powers. Plastic gears are inherently lighter than their metal counterparts. This weight reduction provides several benefits, including lower inertia and energy requirements during operation. When incorporated into machinery, lighter gears reduce wear and tear on adjacent components, such as shafts or bearings. Due to this, industries like aerospace and automotive have heavily adopted plastic for its weight-saving advantages.
Noise Reduction in Machinery
One frequent drawback of metal gears is the noise they generate during operation. Plastic gears, however, have a much quieter running process. Their elasticity absorbs vibrations during rotations, creating smoother, almost silent interactions between gear teeth. This feature is particularly important in environments where machinery sound levels must remain low, such as pharmaceutical labs, as excessive noise could hinder precision processes or disrupt personnel.
Versatility Across Industries
By altering their material composition, engineers can tailor plastic gear replacement parts for diverse applications. Specialized plastics, such as nylon, polycarbonate, and polyethylene, can be used depending on operational needs.
For instance, food-grade plastics are often used in food processing and packaging industries to meet health and safety standards. At the same time, high-performance polymers are ideal for extreme temperature environments usually found in manufacturing plants. This ability to customize gears to specific environments underscores their flexibility and widespread appeal.
Enhanced Chemical Resistance
Certain industries, such as plating and pharmaceutical manufacturing, require materials that can resist harsh chemicals. Even with a protective coating, metal gears can degrade under constant exposure to corrosive agents. Plastic gears, on the other hand, offer excellent chemical resistance without the need for additional coatings. This stability makes them ideal for environments that endure exposure to cleaning agents, acids, and solvents.
Easy Modification and Customization
Creating custom parts with plastics is far easier than working with metals. The ability to mold plastic into intricate shapes and sizes has given engineers greater creativity when designing machinery components. Tweaking gear configurations to fit specialized production lines reduces downtime for installation and adjustments. Customization also opens the door to creating proprietary designs that directly enhance the efficiency and output of a given operation.
Energy Efficiency in Operations
Since plastic gears are lighter and require less torque due to reduced friction, machinery consumes less energy during operation. This energy reduction leads to a marked decrease in utility costs over time. For large-scale operations, such as factories running multiple machines simultaneously, incorporating plastic components contributes to overall energy efficiency.
Environmental and Recycling Advantage
Sustainability efforts in manufacturing and engineering have led to increased scrutiny of waste and resource consumption. Many modern plastics are recyclable, allowing engineers to produce gears from reused materials without compromising durability or performance.
Further, manufacturing plastics uses less energy than metals, reducing the carbon footprint at the production stage. For companies focused on green initiatives, this energy efficiency makes plastic gears an environmentally conscious decision.
Longevity in Harsh Environments
Fluid exposure, temperature extremes, and continuous motion are part of many working environments in food processing or plating industries. Traditional gears made from metal can wear out faster under these conditions, requiring frequent replacements.
Engineers have developed plastic parts to thrive in such environments. Heat-stabilized compositions and added UV-resistant properties allow plastic gears to maintain performance despite prolonged exposure to challenging conditions.
Accelerated Installation and Maintenance
The lighter weight and ease of handling in plastic gear replacement parts simplify installation and maintenance. Metal gears often require heavy lifting equipment or precision alignment tools during installation. Plastic gears, which are less cumbersome, can be quickly set up with minimal disruption. Reduced maintenance requirements also mean engineers and technicians can reduce downtime.
Future Trends in Plastic Gear Development
The evolution of plastic materials and manufacturing technology shows no sign of slowing down. Research on high-strength polymers and bio-based plastics has advanced rapidly, indicating that the next generation of plastic gears will be even more resilient and environmentally friendly.
Industries focused on precision, such as robotics or aerospace, are set to reap even more benefits from these advancements. By staying ahead of the curve and adopting plastic gear replacement parts now, businesses can be better positioned to incorporate future innovations seamlessly.
Driving Efficiency With Modern Materials
The transition from metal to plastic gears reflects a pivotal shift in how engineers approach material selection. Durability, cost-efficiency, and customization no longer need to be competing priorities. Industries maximize performance and stay competitive in an increasingly demanding market by integrating high-quality plastic gear replacement parts into machinery.
The benefits of plastic gear replacement parts include reducing operational noise, resisting wear and chemicals, and enhancing energy efficiency, making them indispensable tools in modern manufacturing and production environments.
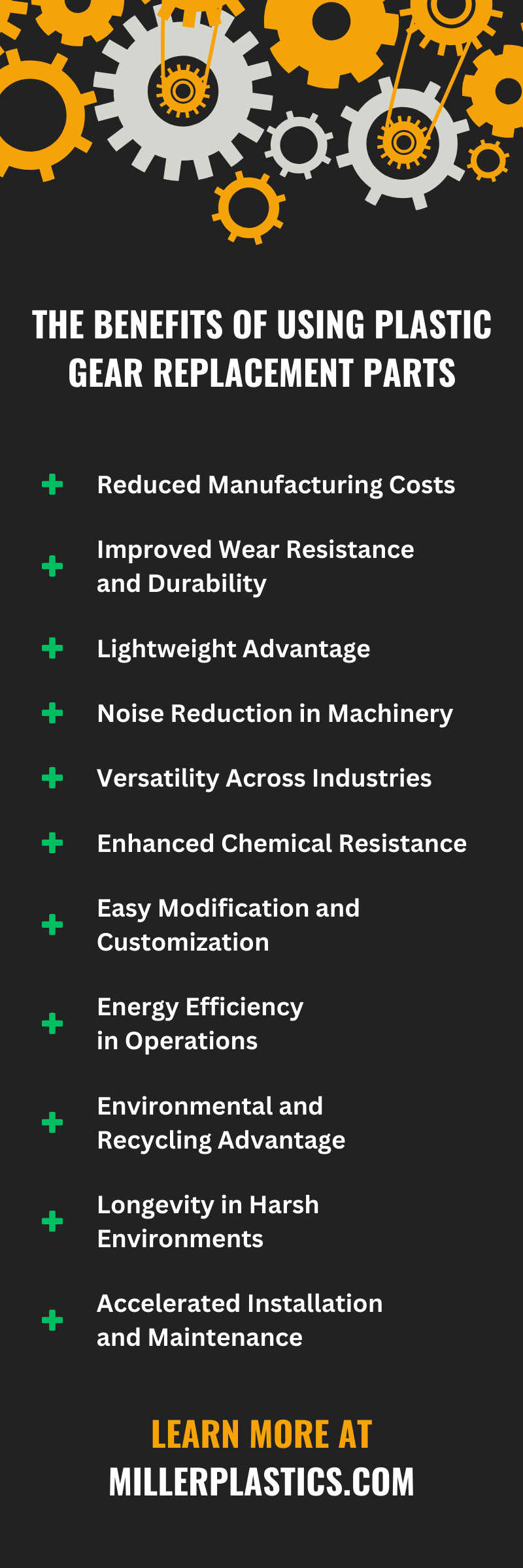