Plastic machining has been a huge part of production for the past few decades, improving productivity for companies around the globe. However, CNC machining has gone through multiple changes throughout the years as it’s improved and become more useful. To help everyone understand this, here’s a deeper dive into the history of plastic machining.
What’s CNC Machining?
CNC machining is the process of creating a product via machines receiving directions from a computer. The basis of the process is subtractive, which means that the process creates products by carving products out of slabs of material. CNC machining uses tools such as drills or mills to create a desired shape out of whatever materials you put into the process.
The Start of CNC Machining
The concept of creating products by carving them out of other materials isn’t new; in fact, it’s thousands of years old. However, the automation of this process is significantly modern and has only grown since the invention first came about.
1949 MIT Project
The first instance of CNC machining comes from a project inside MIT. James Parsons worked on an Air Force Project with MIT to produce helicopter blades and made the first CNC process for the project. The machine would make helicopter blades automatically by calculating the exact measurements and feeding them into a machine using a punched card.
1952 Cincinnati Hydro-Tel
It didn’t take long for others to create more processes that use CNC to speed up production. With the pressure of the Cold War looming, others needed to make more effective production tools. Another MIT collaborator, Richard Kegg, created the first CNC milling machine. However, the patent for the tool wouldn’t come about until 1958.
Punched Tape
These first CNC machines didn’t have the same interfaces we use today, as computers didn’t have the same software or hardware. Computers used punch cards at the time of the creation of these devices. These are cards you would manually create with instructions you would feed into a computer to tell it what to do.
Computer-Aided Design and Machining
The next few decades saw massive improvements to the CNC machining process, but there weren’t any huge developments in how the process operated—until 1972, when computer-aided design and computer-aided machining (CAD and CAM) were first implemented. These two types of software massively improved the interfaces of CNC machining and made it faster and more efficient to create products. By 1989, 3D CAD and CAM were the industry standard and became a worldwide process.
Analog Computing
The change from punch card practices to the newer CAD system didn’t happen in just a few years; there were several advancements needed to make it happen. A big change was the invention and implementation of analog computing. This computing style made it much easier to input commands and operations into the CNC machine to create what you need. However, it wasn’t nearly efficient enough.
Digital Technology
Digital computers were the big turning point in the history of CNC machining, as they opened up more options and increased efficiency for the whole process. Digital computers are capable of more commands and operations at a higher speed, improving automation across the board. That’s why almost every CNC machining process uses digital technology.
Modern Day CNC
Since the evolution of CNC machining using digital technology, the process has undergone more transformations and advancements. While CNC machining remains largely the same, more effective and efficient parts and tools come out every year to improve CNC machining.
Variety of Uses
When CNC machining first came about, it was difficult to use for anything but a few specific items. But the process has drastically changed over the years as technology improves. Nowadays, CNC is useful for many industries and people. Here’s a look at a few of the ways people use it for their benefit.
Making Prototypes
CNC machining is a great production method for creating prototypes of items before you commit to the design. Testing product designs quickly is important, so you can get past the design phase and move on to full production. Many people use CNC plastic milling to create cheap prototypes to test their designs without spending a lot of resources or time.
Efficient Production
The main use of CNC machining is producing a variety of products efficiently and quickly. Production is all about saving money while creating products as quickly as possible, and CNC machining is a great method to accomplish that. While it’s not useful for every type of product, many industries can use it to boost their productivity.
Indirect Manufacturing
Even if CNC machining isn’t useful for making a specific product, the process can be very useful for supplying indirect manufacturing. You’ll commonly see this in industries that need precise equipment. For example, CNC machining can make the sharp blades another machine would utilize to produce the product. Thereby augmenting the production process without directly creating the final product for sale.
Common Modern Uses
While CNC machining is extremely useful for many industries and products, it’s just one of the popular production methods out there. It’s not always the most effective process for every industry and currently sees use in certain industries. Here’s a look at the common uses of CNC machining and the industries that use them.
Production Industries
Commercial and industrial production is the most common use of CNC machining, as these often require precise, durable parts and products at high speeds. You’ll commonly see CNC machining in the automotive and electronics industries, as both industries mass-produce products that require high accuracy and durability.
Military Uses
The invention of CNC stems from military projects with MIT, and that tradition still stands strong. The military still uses the CNC process to create a wide variety of products for their use. Additionally, the military funds products and inventions to further the progress of new CNC technologies to improve efficiency and productivity.
The history of CNC and plastic machining is complex and stretches decades, but the future looks even brighter as the process continues to grow and improve. As it improves, so does every industry’s production capacity—and we’ll all benefit from more efficient production methods.
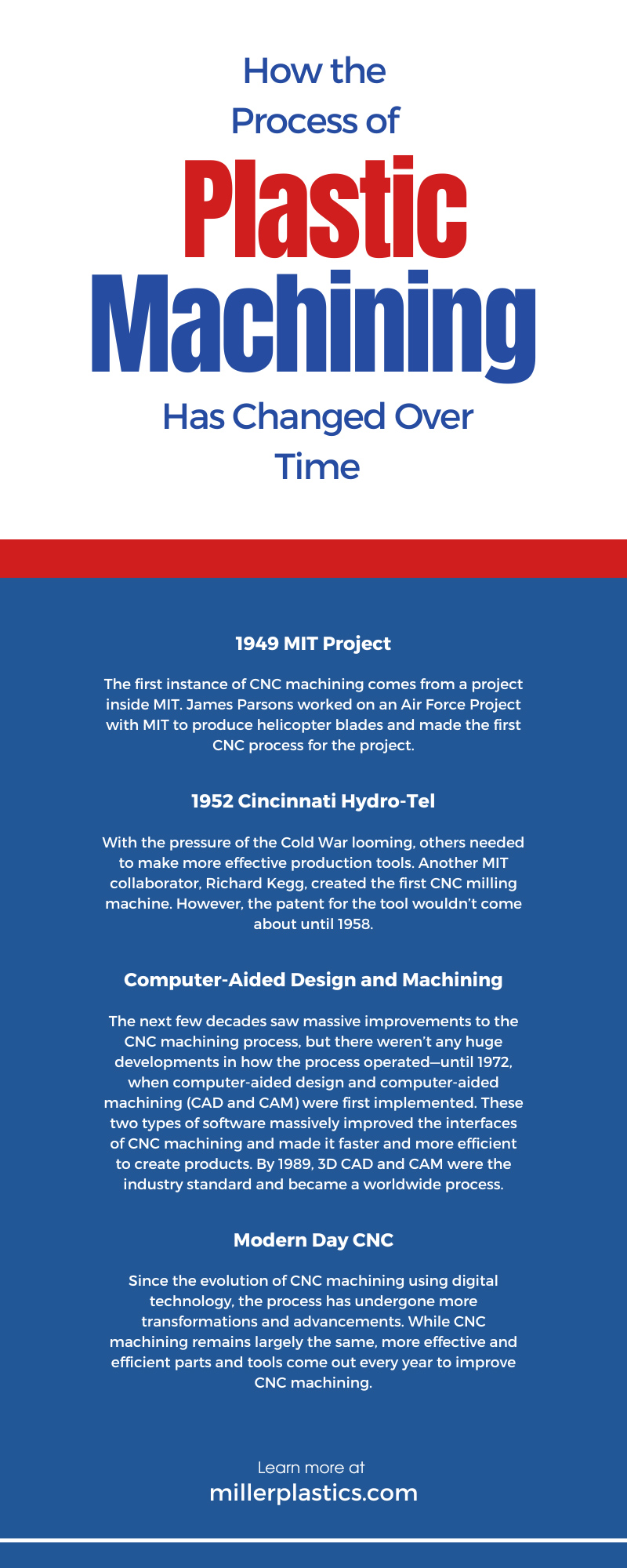